Paint bucket Mould Details
Plastic mold is a global brand established by a high-tech injection mold manufacturer with over 25 years of research and development, manufacturing, and sales experience in the field of plastic barrel molds. Our research and development team has been continuously optimizing and improving plastic paint barrel molds (paint barrel molds) for many years, providing customers and the market with high-quality, efficient, and high-speed plastic paint barrel molds, Help customers achieve the production of plastic paint barrels in the shortest possible time.
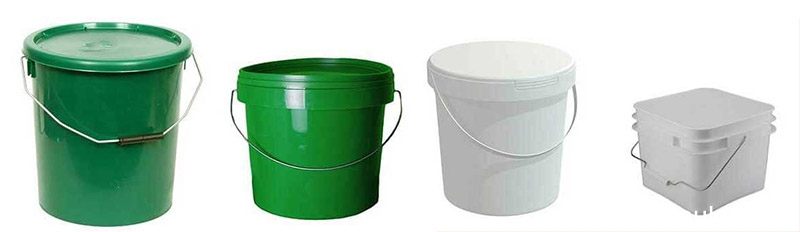
With the increasing competition in the current market, improving production efficiency is crucial. And if plastic coating barrel manufacturers want to achieve long-term development, the most important thing is of course long-term stable product quality and higher production efficiency. Therefore, plastic molds are committed to developing efficient and comprehensive plastic paint bucket mold solutions for customers. We have successfully delivered more than 1000 sets of plastic paint bucket injection molds to customers worldwide, and have gained recognition from customers with comprehensive on-site and after-sales services. We have maintained a long-term partnership with them.
Plastic paint bucket design capability
Quality is the main measure of a product, and the quality of a plastic coating barrel directly affects the competitiveness of the enterprise's products in the market. Therefore, developing and manufacturing higher quality and more competitive plastic paint barrels is a key factor for customers to carry out their plastic paint barrel business. Our mold has established a design team since its inception to provide customers with better quality plastic paint barrels. Our team is dedicated to helping customers design, analyze, optimize, and improve plastic paint barrels with higher quality, aesthetics, and environmental friendliness.
Introduction to Paint Bucket Products
1. The shape of the paint bucket
There are generally three types: square, circular, and elliptical, with the most commonly used ones on the market being round and square, with a capacity of 1L to 35L.
2. Classification of paint buckets
There are two types of buckets, Chinese style buckets and American style buckets. The difference is that there are 2-3 step ribs at the junction of the American bucket and the lid, while Chinese style buckets do not, and the barrel body is relatively smooth.
3. Category of paint bucket
For beginners, they may think that paint buckets and paint buckets are the same product, but their names are different. In fact, paint buckets are a collective term, with four categories: paint buckets, paint buckets, lubricating oil buckets, and engine oil buckets. The difficulty of injection molding increases in order.
4. Testing of paint buckets
Generally, there are tests such as sealing, stacking, dropping, and impact, with the most challenging oil barrel dropping test ranging from 1.5 to 3 meters.
5. Problem with paint bucket recycling
If you want to reduce manufacturing costs, you can use recycled materials. But there are also many types of recycled materials, and if it is a first level recycled material, it is basically equivalent to a brand new material. But if it is a secondary or tertiary material, the color is probably not white anymore. Secondly, the proportion of recycled materials to be added depends on the requirements for the quality of the paint barrel. It would be better to buy ready-made granulation materials. If it is a collection bucket for crushing, it is best to equip it with a granulation line, which will be better.
Introduction to Paint Bucket Mold
1. Types of paint bucket molds
With slider paint bucket, strong paint removal bucket.
2. Ejection mechanism of paint bucket mold
Paint bucket with slider: When the mold thickness is sufficient, the peripheral design prioritizes the use of a sloping top structure design.
Forced demolding mold: When the demolding plate is inverted and there are deep ribs on the demolding plate, splicing is used to solve the problem of deep rib processing. Using two ejections, the center ejects the product onto the stripper plate
3. Design of Components for Paint Bucket Mold
① Cavity bottom: The bottom of the barrel needs to be of a certain thickness, with a bottom of 45mm or more and fixed with screws around it.
② Edge splicing: To ensure the strength of the edge ribs of the barrel, beryllium copper can be used for convenient cooling.
③ Slider bar insertion method: diagonal bars and deep bars exceeding 12mm need to be inserted.
4. Selection of Steel Materials for Paint Bucket Mold
According to actual production requirements, high-quality steel materials such as P20, 718H, H13, and DIN1.2316 are selected, and copper beryllium is embedded in the bottom area and the edge reinforcement area.
5. Paint bucket mold injection system
Cold runner, hot runner, hot runner needle valve, etc. can be used for small capacity barrels, and hot runner needle valve gate can be used for 10-15L barrels.
6. Mold Interchange Design
Interchangeable design of lacquer bucket lid and handle insert to reduce costs.
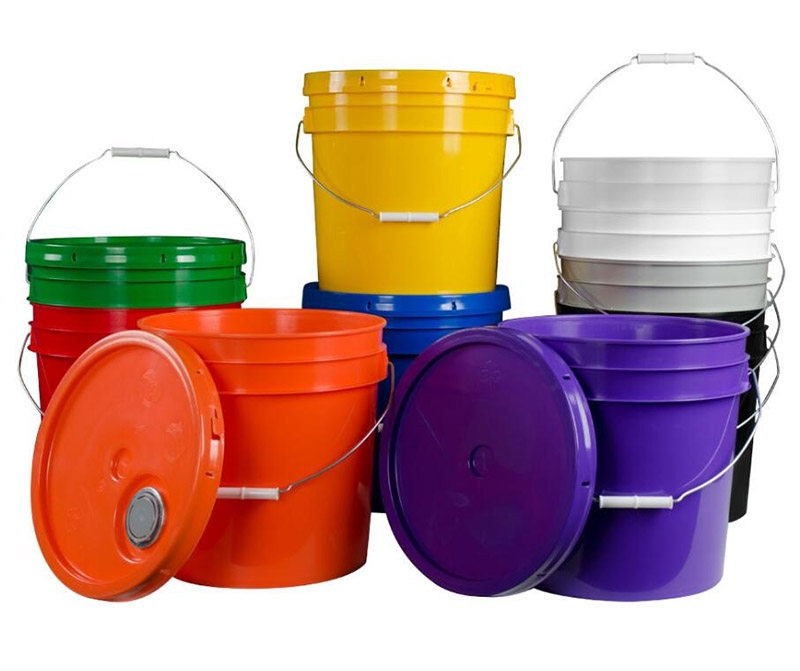
Ability to design plastic paint bucket molds
After solving the quality problem of paint barrels, plastic paint barrel manufacturers will also face a challenge: how to produce plastic paint barrels as efficiently as possible to meet market demand. Don't worry, the plastic paint bucket mold developed by the Xinuo mold design team has high quality, efficiency, and speed, which can solve production efficiency problems for customers. We optimize the paint barrel mold from three aspects: mold structure, mold steel material, and mold cooling time.
Mold structure:
According to the product design along the edge of the plastic paint bucket, slider or non slider design can be selected
According to the sticker requirements for the appearance of plastic paint barrels, automatic demolding or robotic demolding can be selected.
Mold steel material:
The selection should be based on the production requirements of plastic coating barrels, and the mold steel used for different mold components may vary, such as P20, 718H, H13, and DIN1.2316. Ultimately, customers can obtain molds with higher cost-effectiveness.
Mold cooling time:
When the customer requests a shorter cooling time, we have also optimized the cooling design of the mold. In addition to qualified cooling water channels, copper beryllium inserts can also help accelerate the cooling time, with the main areas being the bottom area and the edge reinforcement area.
Plastic paint bucket mold processing capacity
If the design of the plastic paint bucket and mold is good, while ensuring the quality of the mold equipment, the mold processing will be very easy and the size control accuracy will be higher. Due to the high requirements for eccentricity and sealing performance of plastic paint bucket molds, the requirements for machine tools are also high. Our molds have excellent mold processing machinery, including Italy's Fadia high-precision five axis CNC milling machine, Japan's Shaddick mirror spark machine, and so on,
High quality service for plastic paint bucket molds
1.Review of plastic paint bucket project (investment return review and suggestions, feasibility analysis of product molding, recommendation of injection molding machine model...)
2.Design more competitive plastic paint buckets for customers, including analysis and design (drawings required)
3.Weekly mold progress report (to keep you updated on the latest design and processing processes, making it convenient for customers to arrange relevant work in a timely manner)
Quick response (such as remaking damaged mold components)
4.Training support (providing training on mold operation, maintenance, and mold adjustment techniques for customer employees...)
5.Maintain and support customized special services during the warranty period
Provide assistance in quality testing of different plastic paint buckets (weight tolerance, concentricity testing, stacking, drop testing, sealing testing...)
Send Your Inquiry Now