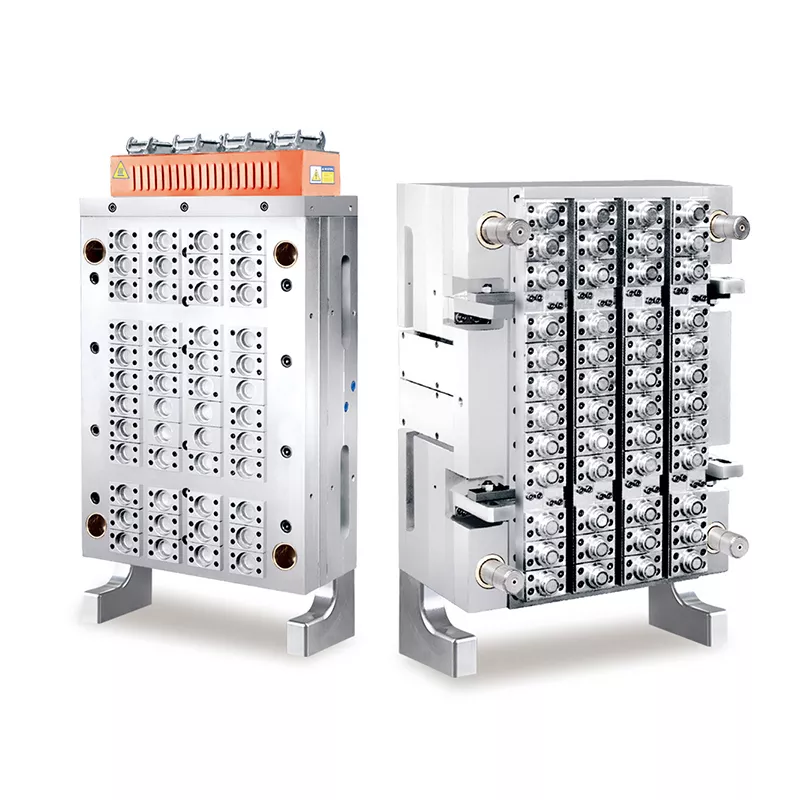
Blow molding mold is a mold tool specifically designed for producing plastic blow molded products. Blow molding is a plastic processing method that involves heating, melting, and blow molding thermoplastic materials, which can produce plastic products with cavity structures.
Blow molding molds typically consist of two parts: an inner mold and an outer mold. Internal mold is a mold used to shape the internal shape, usually with a cavity structure, such as bottle mouth, bottle body, etc. The outer mold is used to fix and maintain the shape of the inner mold, usually with grooves or bosses corresponding to the inner mold.
In the manufacturing process of blow molding molds, plastic particles or blocks are first heated to a molten state, and then the melted plastic is injected into the inner mold. Then, the plastic is blown open by air pressure to fill the entire inner mold cavity, ultimately forming the required shape and size. To ensure that the mold has hardness, wear resistance, and corrosion resistance, blow molding molds are usually made of high-temperature alloy steel materials.
Blow molding molds have the characteristics of high precision, high durability, and stability, which can produce high-quality blow molded products. It is widely used in fields such as food packaging, bottled beverages, cosmetics, pharmaceuticals, etc., to meet people's needs for plastic products of various shapes, specifications, and functions. The design and manufacturing of blow molding molds need to consider factors such as product structure and size requirements, as well as production efficiency and cost control, to ensure the production of blow molded products with good quality and economic benefits.
1、 Principles of Blow Molding Mold Processing
Simply put, the processed raw materials are placed in a split mold, compressed air is introduced to make the mold closely adhere to the inner wall of the mold, cooled, and demolded.
2、 Blow molding process method
According to different processes, blow molding processing can be divided into two methods: extrusion blow molding and injection blow molding.
A. Extrusion blow molding: The resin is softened by an extruder, and a tubular shaped embryo is extruded. It is placed in a blow molding mold, expanded by compressed air, and then cooled to obtain a hollow product that is the same as the mold.
B. Injection blow molding: By using an injection molding machine, the material is injected into the mold to obtain a tubular shaped embryo. After opening the mold, the embryo is placed in the core mold, closed while hot, and compressed air is introduced to expand the embryo. Through the inner cavity of the mold, the same hollow product as the mold is obtained.
3、 What products can be produced by blow molding processing?
According to different blow molding processing methods, the products produced by the two will also be different
A. Extrusion blow molding: It has a wide range of uses and can be used to produce large hollow products, such as barrels and water tanks for industrial containers.
B. Injection blow molding: suitable for producing smaller, larger batches of products, such as mineral water bottles.
The blow molding process can not only produce the above, but also products such as pallets, roadblocks, double ring barrels, kayaks, etc.
4、 Selection of raw materials for blow molding processing
A. HDPE: High density polyethylene, is one of the commonly used materials in blow molded products. This type of plastic is suitable for producing various products, such as heavy metals, glass, packaging paper, coolers, oil tanks, industrial drums, etc., and has a wide range of uses. Its material is semi transparent, with good tensile strength, strong plasticity, non-toxic, and is also a relatively reliable material.
B. PP: Polypropylene is also a commonly used resin, suitable for high temperatures. Its texture and HDPE are both semi transparent, with high hardness and low density, and it also has certain advantages. It is commonly used in medical devices, chemical containers, pharmaceuticals, etc.
C. PET: Polyethylene terephthalate, a common resin in daily life, has good physical and mechanical properties, suitable for various bottles, such as cola bottles, and can also be used as electrical components. The color is mostly milky white or light yellow, and the surface is smooth and glossy.
D. LDPE: High pressure low density polyethylene, which is the lighter variety of polyethylene resin. It has good transparency and softness. Commonly used in clothing, food seasoning, and also in blow molded plastic bag films.